Big Blue Blog - Wipes
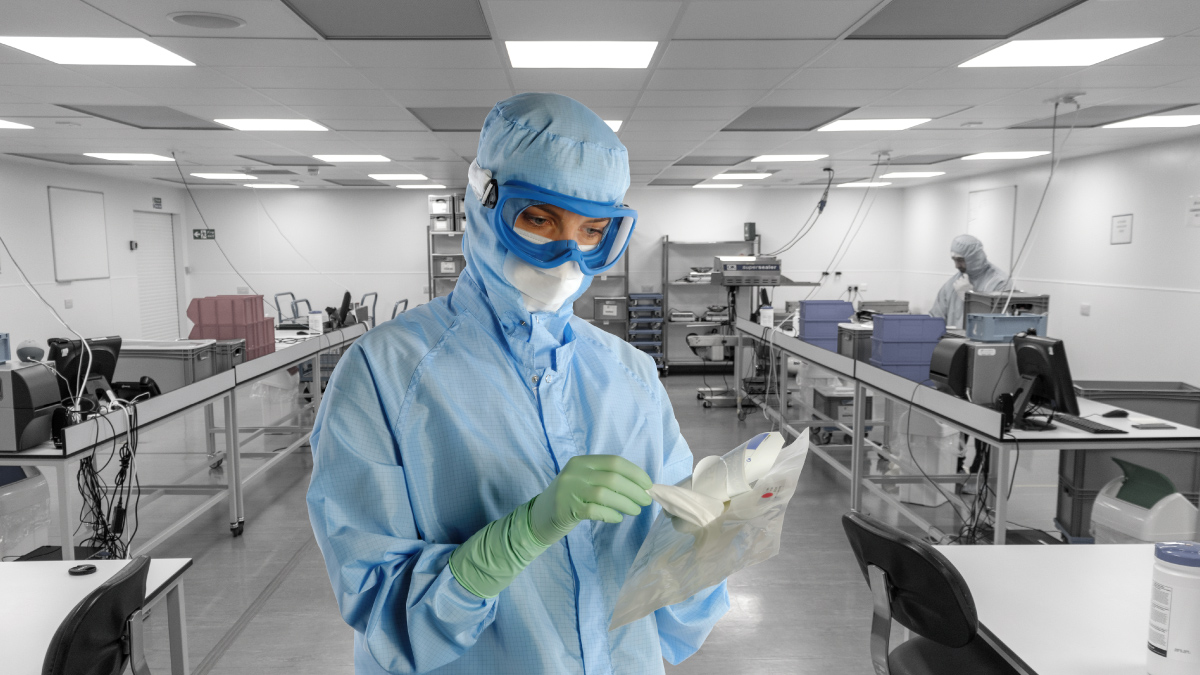
Wipes are used in all cleanrooms as one of the main cleaning methods.
They are chiefly used to remove the invisible contamination of particles and fibres 50µm and smaller. Uses include the wiping of surfaces such as bench tops, the cleaning of small pieces of equipment such as bottles or trays, wipe down (or preparation) of items or their outer packaging before being taken into the cleanroom or isolator and glove wiping for cleanroom staff. Wipes may also be needed to absorb and pick up spillages which occur during the production process.
Wipes may be used dry but are much more efficient in removing contamination when dampened with cleaning or sanitising solutions.
In all instances wipes for cleanroom use must not introduce significant particulate or fibre contamination into the controlled areas.
In a few operations, notably surface finishing, re-usable wipes may be employed which can be re-processed by a cleanroom cleaning and decontamination plant, however the majority of cleanroom wipes are discarded after a single use.
Wipes are available in a very wide range of materials, presentations and price and so it is important to select the product which will satisfy cleaning requirements in the most efficient and cost effective manner.
The main factors to consider when comparing cleanroom wipes are;
- Physical properties
- Wiper materials
- Wiper edge finish
- Wiper size, fold and packaging
- Wiper cleanliness and sterility
- Dry or pre-wetted wipes
- Supporting documentation
- Cost
Physical properties
Wipes are made from materials which must have good surface contact so that particles can be pushed free from the surface being wiped.
Wipes must not be abrasive or cause damage to the wiped surface. Wiper materials must be able to withstand the cleaning operation without tearing or suffering surface breakdown resulting in the loss of particles and fibres from the wipe.
The wiper materials must be compatible with any chemicals with which they come into contact and not be dissolved or otherwise broken down by cleaning agents or production chemicals. In many applications the wipe should not contain materials which can be released in solution during use such as ionic chemicals or endotoxins.
Where the wipe will come into contact with hot surfaces it should have sufficient heat resistance to withstand this without damage. If control of electro-static dissipation (ESD) is a requirement the wipes must have good ESD properties.
Cleanroom wipes should have good sorption. This indicates the volume of liquid the wipe will absorb in relation to its weight and the time taken to do this. Good sorption properties will allow a wipe to quickly take up a spillage and will also enable an impregnated wipe to cover a large area without drying out.
Wiper materials
Cleanroom wipes are usually manufactured from knitted or non-woven fabrics however woven fabrics and foam material wipes are also available.
Wipes specified for use in high grade cleanroom areas are usually produced from knitted filament yarns, usually polyester or nylon, and these include those made from microfibre yarns which give increased surface contact area.
Filament polyester is low shedding and can be effectively cleaned and decontaminated before use. It will withstand sterilisation by gamma irradiation or autoclaving without damage.
Knitted fabrics are very pliable and this allows the wipe to maintain a high contact area and to be easily folded for use.
Knitted fabrics generally have high sorption properties which increase with fabric weight and this will further increase when the wipe is produced as a double layer (2-ply).
Non-woven materials are usually a combination of polyester and cellulose or polypropylene and are normally specified for use in lower grade cleanrooms, less critical wiping operations or spill control. The materials can be sterilised for aseptic area use and have good sorption.
As wipes are usually a disposable product it is preferable to use materials which can be re-cycled.
Wipe edge finish
Wiper fabric is produced in large rolls and must be cut down to produce individual wipes. The cut edges of the wipe can produce particles or fibres and to reduce this source of contamination the wiper edges can be sealed using various methods including sealing with heat or laser and heat rolled edges.
Wipe size, fold and packaging
Wipes are available in an extensive range of sizes and presentations.
They may be presented flat in a layer with each wipe being removed by the user. Wipes may also be folded so that they are interleaved and removing a wipe pulls the start of the next wipe from the pack.
Wipes can be sourced on rolls, in tubs, or in individual packs and most packaging will incorporate a re-sealing system, especially if the wipes are pre-wetted with a volatile chemical such as an alcohol or solvent. Several layers of packaging may also be utilised to facilitate transfer into a high grade area.
Whatever packaging is employed clear and adequate labelling must be used which is not damaged by wiping with alcohol or other solvents and the packaging material must not produce significant fibre or particulate contamination during opening.
Whenever possible packaging and containers for wipes should be made from materials which can be re-cycled.
Wiper cleanliness and sterility
Knitted, woven and non-woven fabrics for wiper manufacture are produced in large industrial plants and the fabrics will become heavily contaminated with fibres, particulate, micro-organisms and chemicals from the production process. This contamination is increased when cutting the wipes to size and if they are to be used in an environment where this would present a problem, the wipes must be cleaned and decontaminated before use.
This is normally achieved using a cleanroom cleaning and decontamination plant and the process is highly successful in decontaminating woven or knitted polyester wipes. It is not possible however to decontaminate cellulose wipes in this way.
Suppliers of cleanroom wipes will be able to provide full data on particulate and fibre levels of different wipes and information on chemical contaminants such as ionic materials and endotoxins.
A wide range of sterile wipes is available and are usually required in aseptic manufacturing processes. Wipes are routinely sterilised by gamma irradiation to achieve a sterility assurance level (SAL) of 10-6.
Dry or pre-wetted
Cleanroom wipes are available either dry, or pre-wetted with a cleaning or sanitising solution. All types of wipe materials can be supplied in these formats.
If wipers are to be primarily used to absorb spillages then dry wipes are used. In cleaning applications however, wiping is carried out using a liquid to dampen the wipe to improve particulate removal.
If an anti-microbial solution is used a layer of sanitising solution will also need to be deposited by the wipe to kill or inactivate micro-organisms which have not previously been removed.
A solution can be applied to a dry wipe just before use using a dispenser or spray however the chemical must be prepared in advance and will not be evenly absorbed by the whole wipe giving uneven application.
Pre-wetted wipes provide the simplest option and are dosed with a specified volume of chemical before the pack is sealed. This allows the impregnated chemical to be evenly absorbed and gives an optimum chemical loading on each wipe.
Pre-wetted wipes can be sterilised following chemical dosing so ensuring both wipe and chemical are sterile at the point of use.
When volatile chemicals are used to pre-wet wipes the packaging must be effective in stopping any chemical evaporation from the pack during storage and should also incorporate a re-sealable opening to stop loss of chemicals once the pack is opened. Sterilised wipes, pre-wetted with alcohol are used within high grade pharmaceutical cleanroom areas. For such applications, pre-wetted wipes have significant advantages over the use of similar dry wipes and alcohol discharged as an aerosol from a canister. Such canisters deliver vast quantities of alcohol particles into the cleanroom which remain airborne for extended periods of time. These particles are likely to be ‘counted’ by any particle counters present in the cleanroom and will consequently record artificially high levels of airborne particles. Additionally, such particles will be readily inhaled by personnel present within the cleanroom with significant associated health concerns.
Supporting documentation
When inexpensive, non-sterile wipes are utilised for wiping operations a basic product specification is sufficient which identifies the wiper material, contamination levels and general product information on quantity and presentation. If pre-wetted wipes are being used then a materials safety data sheet (SDS) will also be supplied.
For more highly specified wipes used in high grade areas additional documentation will be required to confirm the acceptability of the wipe before use. This will include full batch traceability for each individual wipe pouch, details of particulate and chemical contamination levels, confirmation of pouch materials, certificate of irradiation when sterility is required and colour-change detex irradiation labels on each pouch. A SDS will be required for all impregnated wipes. Full documentation is usually supplied with each box of wipes and this may need to be included in cleanroom product batch records to satisfy regulatory requirements.
When wipes are required for critical areas the user will wish to audit the wipes production facilities and the supplier will maintain records providing full batch traceability for the whole supply chain.
Cost
Cleanroom wipes are available within a very wide price range. The material used for the wiper, edge finish, wipe size and presentation, packaging, level of cleanliness and supporting documentation all affect the final cost. Sterilisation and pre-wetting also significantly increase costs.
This means that the more highly specified and controlled the wipe the higher the cost and so it is important to ensure that the correct wipe is clearly identified for each area and each wiping operation.
Use of wipes
Each cleanroom cleaning plan will clearly identify the specific use of wipes however there are some useful guidelines to adopt when using wipes in any cleanroom.
- The cleaning plan and standard operating procedures (SOPs) will indicate which wipes should be used for each cleaning application and only the specified wipe should be used. This should also be made clear to contractors or engineers who may be operating in the controlled areas.
- When used for absorbing spills a dry wipe is simply removed from the container and applied to the spilled liquid. Once absorbed into the wipe the wipe is discarded in a safe manner according to the area procedures. A further dry wipe should then be used to wipe over the area and remove any residual moisture.
- If cleaning or sanitising chemicals are to be applied to dry wipes the chemical should be dispensed onto the wipe and not onto the surface to be cleaned. This minimises the possibility of chemical aerosols contaminating the cleanroom.
- If pre-wetted wipes are used then care should be taken to ensure that once opened the wipes container is re-sealed between uses to stop loss of impregnant through evaporation. When pre-impregnated wipes containers have been opened and re-sealed several times it is possible that evaporation has occurred and the wipes are no longer wetted to the required level. In this case the wipes should be discarded.
When using wipes to decontaminate critical areas it is good practice to fold the wipe to provide eight separate cleaning faces. The wipe should be used in single overlapping strokes with a maximum of eight passes (one for each folded face) per wipe (as shown in the sequence of illustrations 1-5 below).
This technique will maximize particle removal and the surface area covered will depend on the size of the wipe and the quantity of liquid absorbed.
- When wipes are being used to apply a sanitising solution care should be taken to ensure that sufficient chemical is transferred to the surface from the wipe and that it is evenly distributed. Adequate disinfection will not take place without the correct application of sanitiser.
- Wipes must be discarded correctly as indicated by the cleaning plan. Any wipes containing chemical residues either from spillages or chemical impregnants must be collected for safe disposal as indicated by the SDS, Environmental and Health & Safety considerations.