Big Blue Blog - Cleanroom Cleaning - General Considerations - Part One
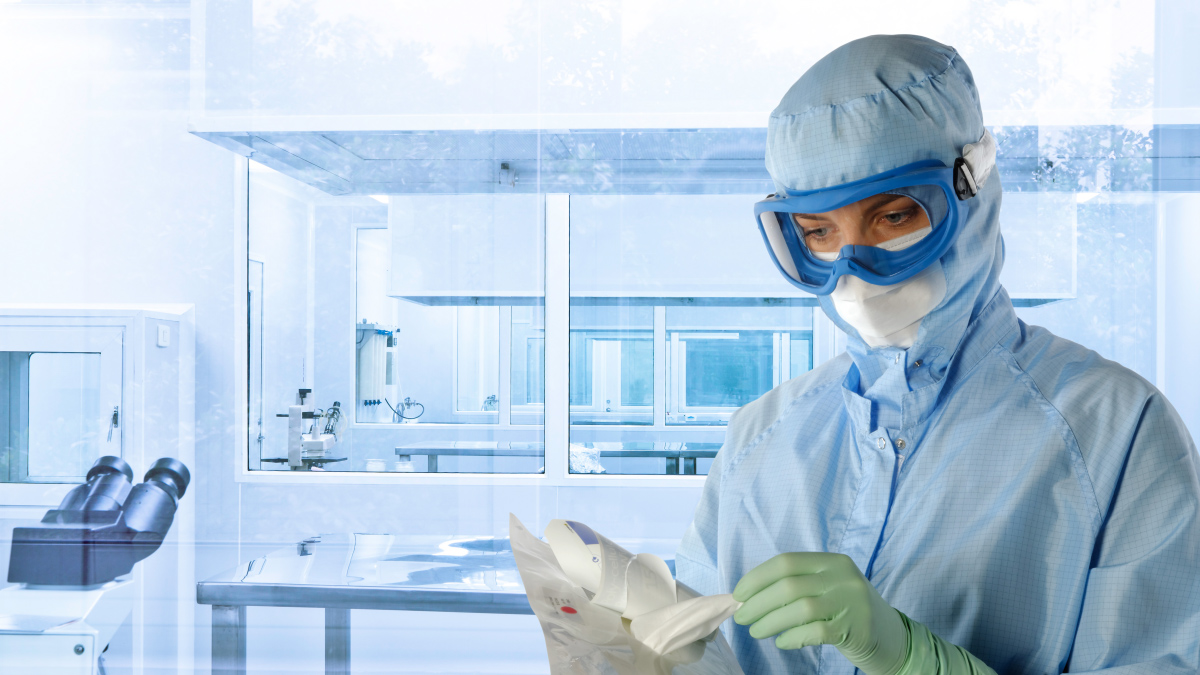
Visible contaminants in the cleanroom can be controlled by basic cleaning and housekeeping methods.
Very large contaminants such as discarded packaging or cleanroom disposables can be placed in a disposal bag and carried from the area. Disposal containers should be placed in areas where they can be frequently emptied. Reusable cleanroom clothing can be removed and placed in designated containers for collection and reprocessing. These containers should not be large enough to allow several days of discarded items to accumulate and should be emptied using a technique which minimises dispersion of particulate into controlled areas.
Large visible particulates and fibres are quickly deposited by gravity and so are normally found on horizontal surfaces. This material can be readily removed using cleanroom compatible vacuum cleaning, the material being lifted from the surface by the airflow and collected for disposal.
Microscopic contaminants, containing both viable and non-viable particles range from approximately 50µm down to <1µm in size and are affected much less by gravity. This material will be deposited on horizontal surfaces but will also become attached to walls, ceilings and equipment. The cleanroom airflow (vertical or horizontal unidirectional airflow or turbulent flow) will also affect the distribution and deposition of these particulates.
All surfaces in a cleanroom should be as smooth as possible with minimal sharp corners as rough surfaces and inaccessible angles are more likely to hold fine particles making them difficult to remove.
Microscopic particles and fibres on cleanroom surfaces may be attached by physical, chemical and electrical forces the main force being the physical intermolecular force known as London-van der Waals. Particles of this small size cannot be removed by dry vacuum cleaning as this method has insufficient energy to overcome these adhesive forces.
This material must be dislodged by direct physical contact and this is usually achieved by mopping or wiping. The material from which these mopping or wiping products are made will affect their particle removal efficiency - the greater the contact area the better the removal effect.
Particle removal is significantly improved if a liquid is used to aid the process which allows some of the particle to surface bonding to be broken. Suitable cleaning liquids not only increase the physical removal efficiency but may also dissolve or suspend the contaminants.
Water, surfactants or solvents may all be used in this way to dampen wipes and mops and improve particle removal. Wet cleanroom compatible vacuum cleaning, which is more efficient than a dry vacuum system, may also be employed for appropriate surfaces such as large floors.
Water used for cleaning or chemical dilution should be at a purity which is acceptable in the area being cleaned and must not be a source of micro-organisms or chemical residues.
In any cleanroom cleaning programme it is therefore necessary to first remove the visible contamination before the removal of the microscopic contamination. The removal of visible contamination is sometimes referred to as “cleaning” and the subsequent removal of microscopic particles as “decontamination” and this can be a helpful distinction during staff training.
As part of the cleaning process it is often necessary to use antimicrobial chemicals which are used to kill or inactivate any micro-organisms remaining after cleaning. These are usually referred to as disinfectants or sanitisers and are available in a wide range of formulations.
ISO 14644-5 Operations gives limited guidance on cleanroom cleaning but the cleaning system and materials will be largely developed to suit the requirements of each cleanroom facility.
Significant factors which will influence the cleaning programme;
- The product being manufactured
- The cleanliness classification(s) of the facility
- The requirement for microbiological control
- The size of the facility
- Hours of operation
- Production equipment and machinery
- The number of staff
- The types of contaminant present
- Health and safety requirements
- Availability of trained cleaning staff
- Cost
The product
The product being manufactured must be protected from damaging contaminants. This may range from large fibres e.g. for optical or surface finished products to microscopic particles harmful in microelectronics manufacturing. Biomedical products will be especially damaged by viable particles.
The cleaning methods and materials chosen must help to minimise product contamination and at the same time not themselves produce any damaging effects or residues.
Cleanliness classification
The established cleanliness classifications for each area will guide the requirements of the cleaning programme. The more highly controlled areas will usually warrant the most frequent and intensive cleaning methods.
Non-classified outer areas should also be included in the cleaning programme and a high standard of housekeeping and cleaning in areas adjacent to the controlled areas will assist in overall contamination control.
Microbiological control
When the cleanroom is producing biomedical products the main emphasis is on the control of micro-organisms and the highest level of control is required during aseptic manufacture.
This requirement will influence the cleaning methods and materials. Micro-organisms form part of the microscopic contamination and so great care must be taken to ensure the removal of viable organisms during this stage of cleaning.
Anti-microbial chemicals will be required as part of the cleaning process and all cleaning products and materials will be sterilised before use. Following cleaning no residues should be left on cleanroom surfaces.