Big Blue Blog - Standard Cleanroom Coverall GMP Gowning
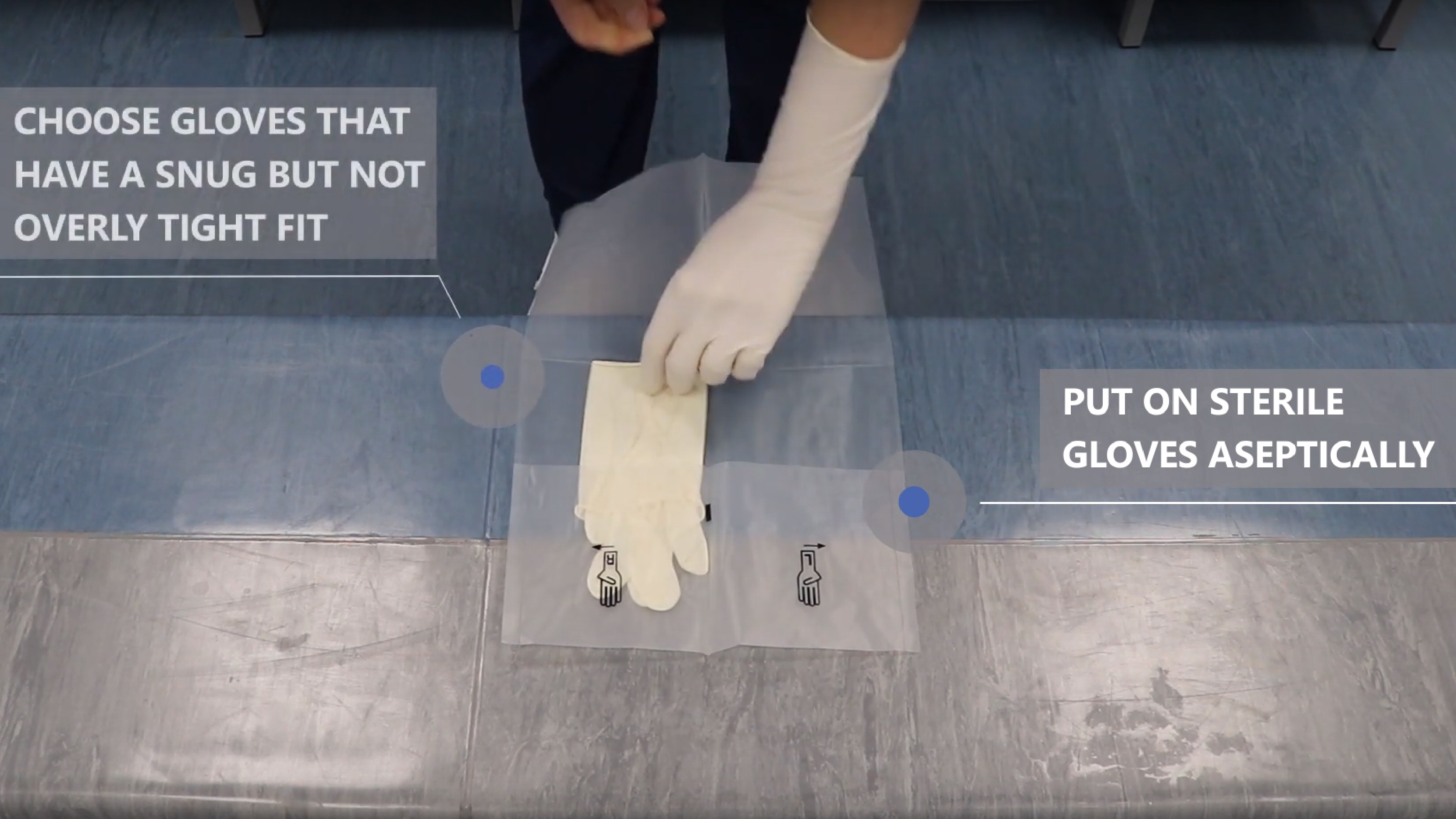
This video shows a generic GMP compliant procedure, suitable for use with a cleanroom coverall.
Our latest video takes you through a step-by-step procedure for standard cleanroom coverall GMP gowning. This includes what to do before entering the area, prohibited items, and how to correctly prepare for entrance into the cleanroom.
Please note that this is for guidance only and that local procedure should be fully validated.