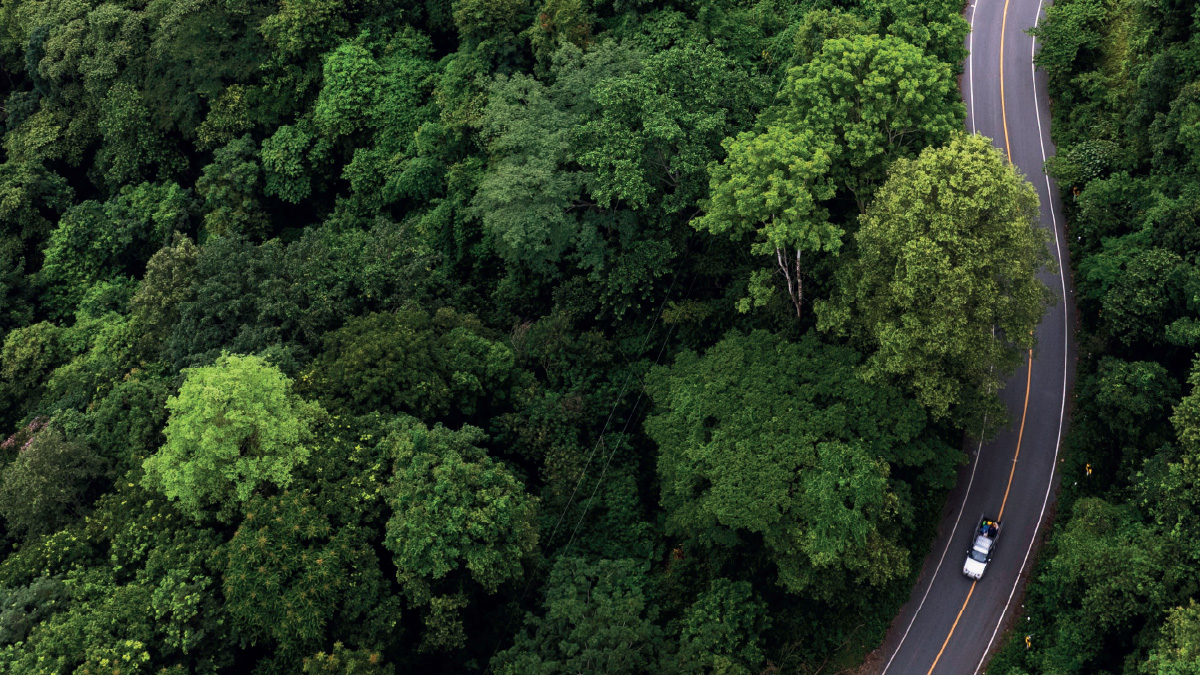
NewsCleanroom18.06.2025
Micronclean Cuts CO2 Fleet Emissions by 90% with Switch to HVO
Micronclean has introduced Hydrotreated Vegetable Oil (HVO) as the primary fuel for its transport fleet based in Skegness and Louth, delivering a projected 90% reduction in CO₂ emissions.
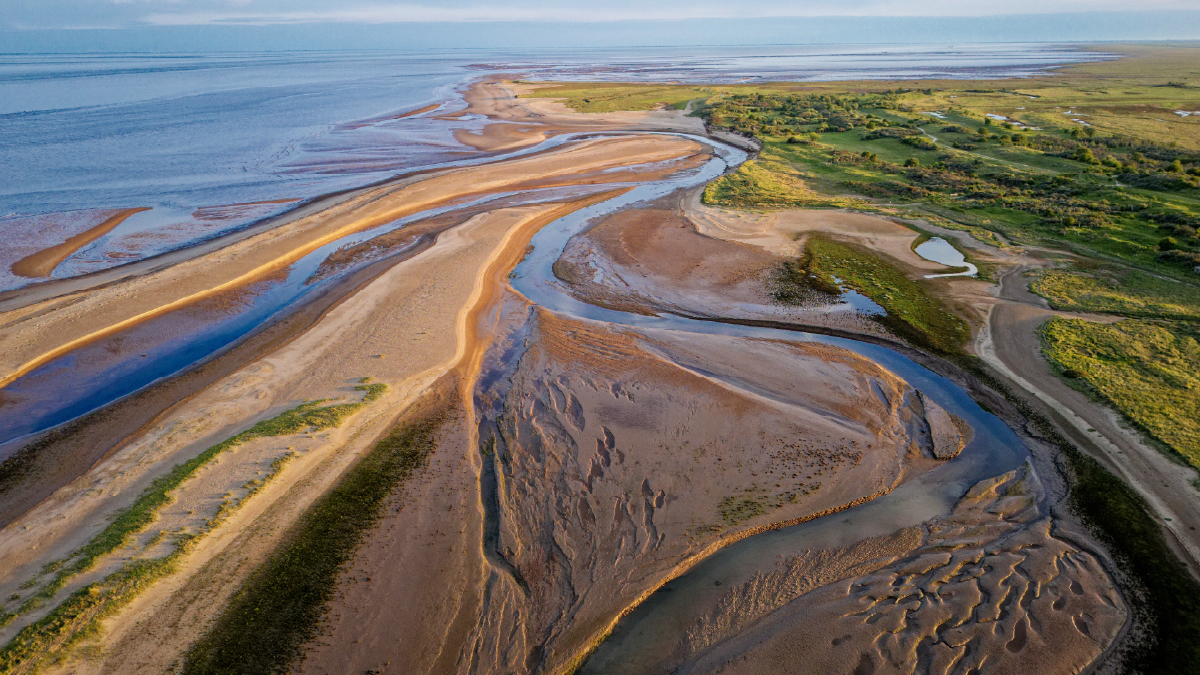

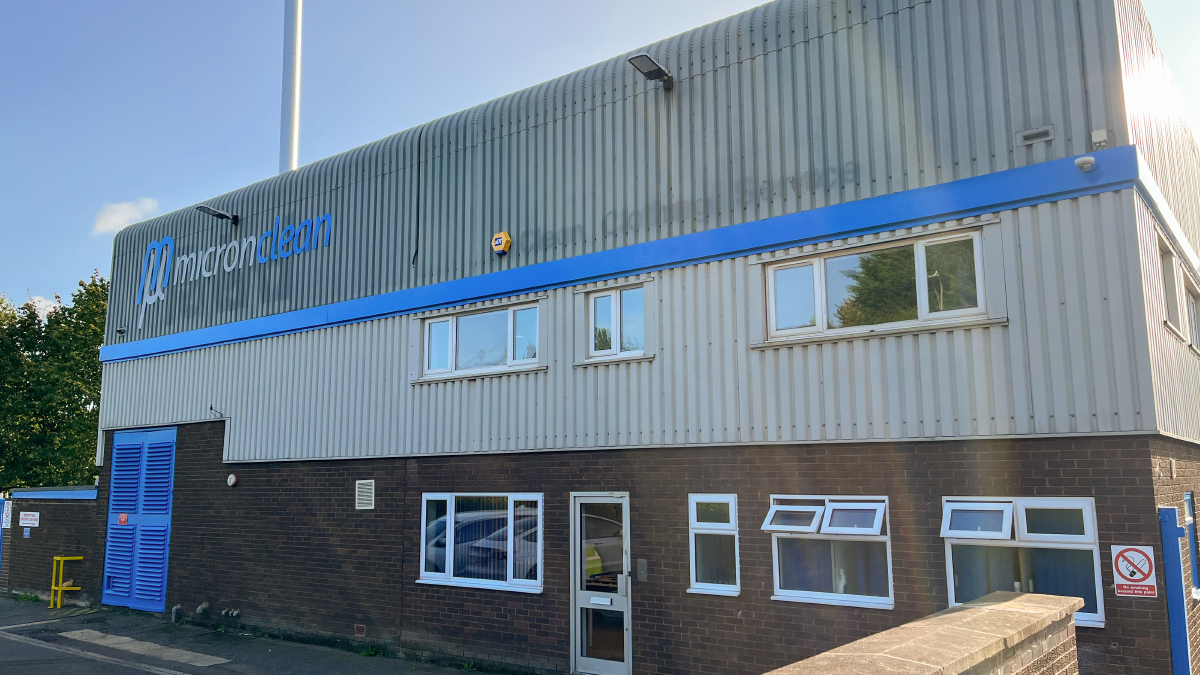
Micronclean Consolidates Business Operations with Strategic Withdrawal from Heavy Industrial Workwear Market
NewsPPE/Textiles31.10.2024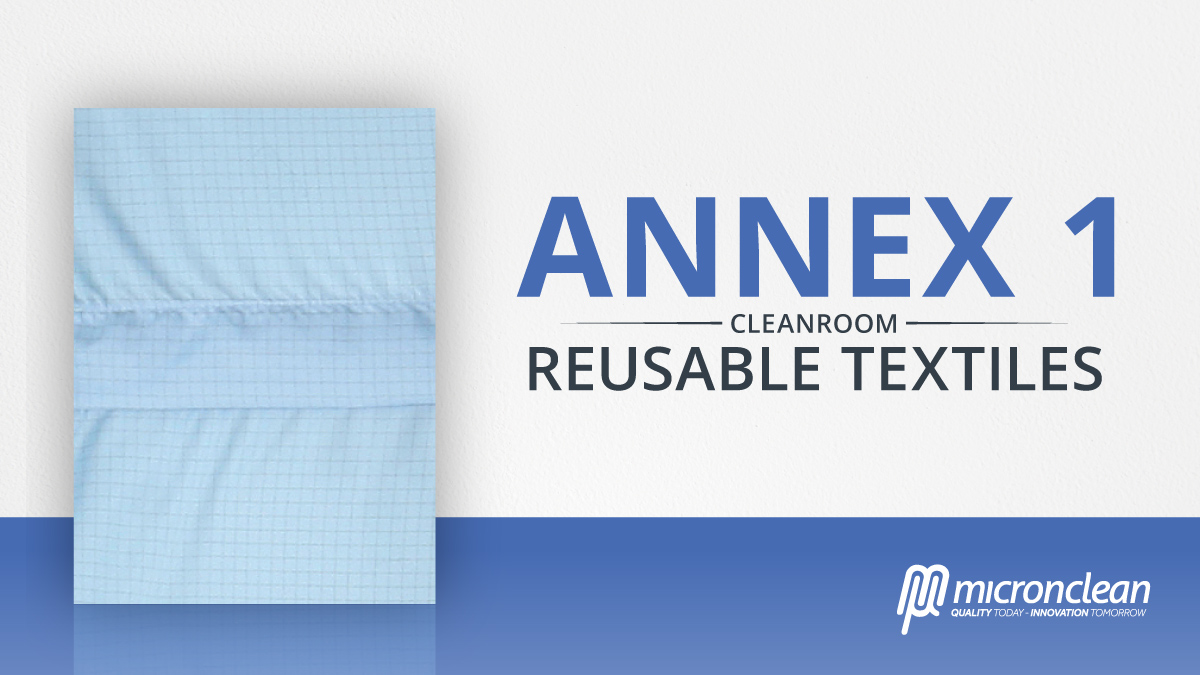
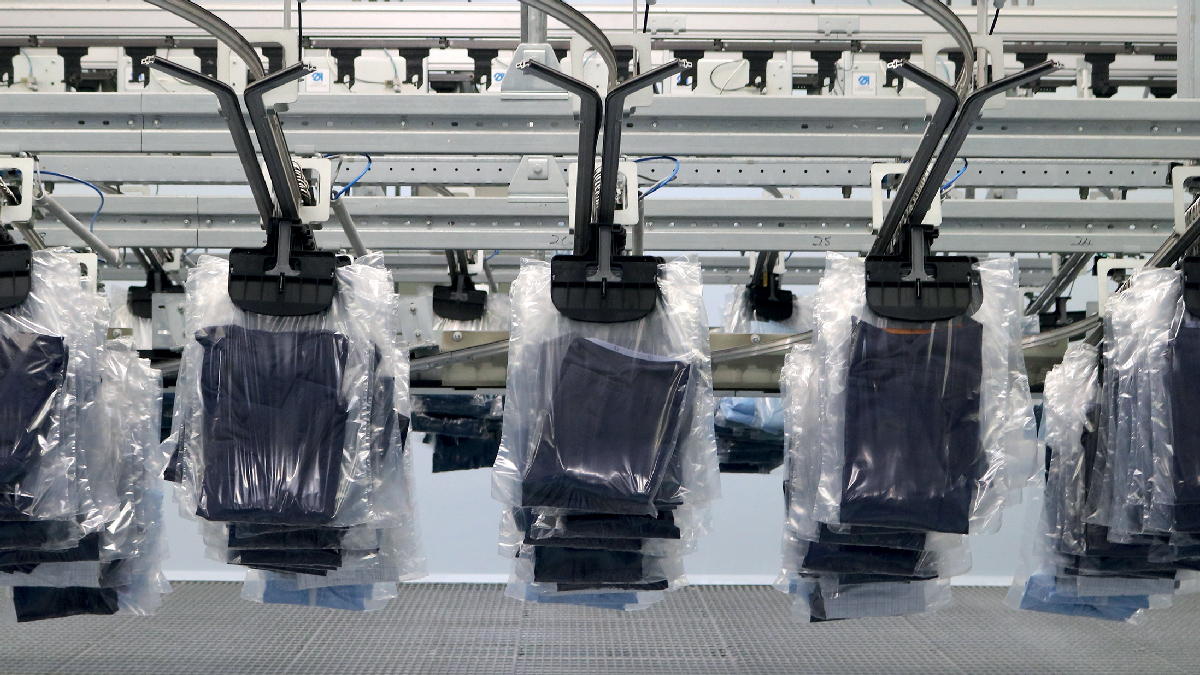
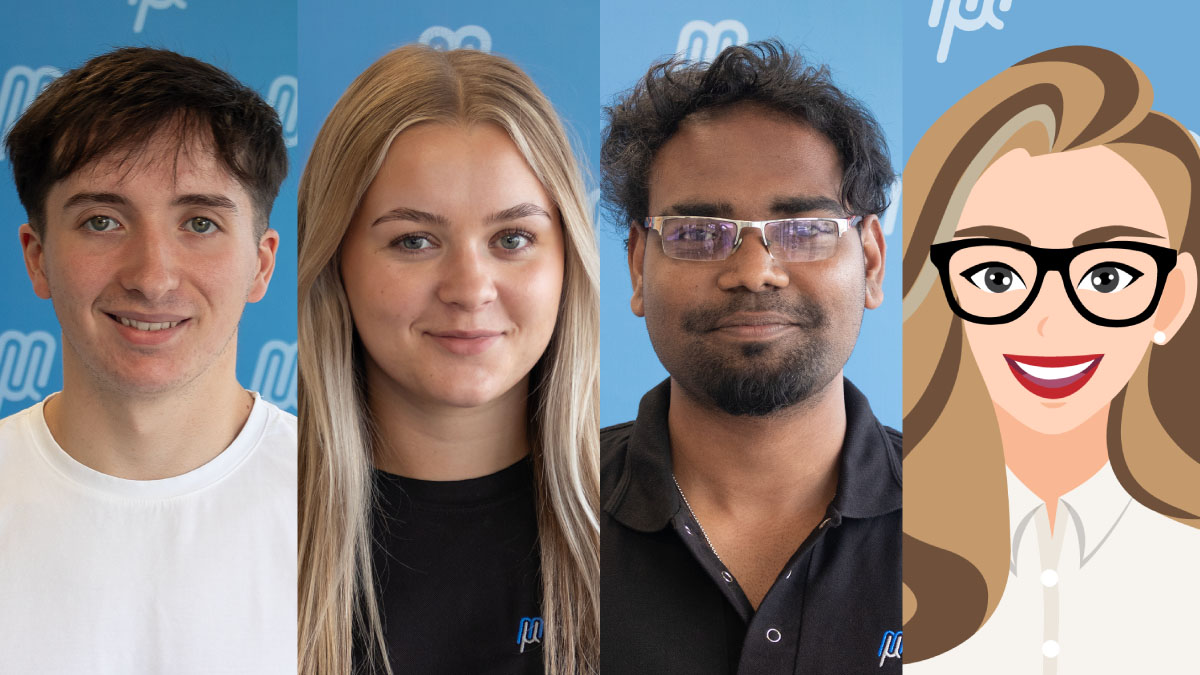